Description (Phenomena, Details, Ways to Reproduce the Problem):
-
During the stage of checking the calibration board position and point cloud quality, clicking “capture live” results in an error stating “Unable to find the calibration board in the image. Please check the mounting of the calibration board. Proceed anyway?”
-
However, when using the intrinsic parameter tool function in Mech Eye Viewer, everything appears normal.
-
After manually drawing an aid circle to check the intrinsic parameters, it indicates a pass.
-
However, proceeding with the calibration to collect calibration images in the pyramid path results in all collected data being incorrect. The error message “Unable to obtain move information from the current calibration board image”
- Methods tried or troubleshooting record
- Tried to reset to factory intrinsics parameters in the Mech Eye Viewer 2.3.0. It show “Please retry or contact Technical Support”.
Hello,
The calibration board may not have been chosen correctly here. You can find the recommended calibration boards for each camera model from the camera material table at the download center:
Download Center: Camera Materials
Also, please refer to the Hand-Eye Calibration Process section of the user manual for step-by-step guide: https://docs.mech-mind.net/en/suite-software-manual/latest/vision-calibration/select-calib-process.html
The calibration board is provided from your side. The camera model is NANO and is suitable for my calibration board OCB-20. I realized that the customer had set the offset of the intrinsic parameters. May I know how to check if they have modified the settings? Is it from the extri_param.json file, as shown below?
Can I give your email address to my colleague so they can contact you?
They may need your project file and do remote screen control to troubleshoot the problem.
Hello, it seems the detection process of calibration board in 2D image failed. Could you please send us the extra calibration files in Mech-Vision? We can use it to anaylze.
Yes sure.
My email address : zheng.yang@jm-vistec.com
Let me know the time for the remote support.
Hi,kong I hope you haven’t been waiting too long for my response.
please take a look at the following image.
The reason for the inability to recognize is that the small circles on the calibration board interfered with the automatic detection of the calibration board.
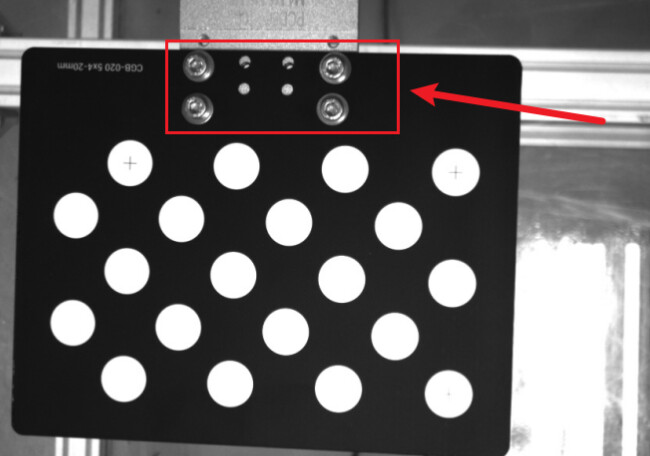
You can solve the problem by covering this position or painting the nut black.
Okay, thanks. After covering the black nut on the calibration board, the robot calibration is now working normally.
Could you please explain why this issue occurred? Is there a difference between the intrinsic check in Mech-Eye View and Mech Vision?
The Mech-Eye View check was okay, but the Mech Vision check failed. Additionally, after manually drawing an aid circle to check the intrinsic parameters, it indicated a pass. However, the subsequent automated calibration failed.
Due to the extended overall exposure time and the overall reflection of the screws, misidentification occurred when recognizing the white circles on the calibration board.
I believe that by appropriately reducing the exposure, it’s also possible to mitigate this issue.
Of course, we can optimize the recognition function in the future to minimize interference as much as possible.