Utilizing the picking relaxation (Picking Relaxation) enables the robot to pick a lot more items without running into collisions or singularities.
With the latest Viz Update (1.8.2) the singularity detection become a lot better, but leads to many iterations to find a feasable path when close to singularities (very long planning time, sometimes over 30 seconds). Using the robots internal singularity avoidance was my solution until now, but this was sometimes leading to unexpected behaviour. Disabling singularity avoidance completely also seems not possible anymore in 1.8.2.
In order to fully use the new singularity detection and path planning, it would be great to have the relaxation for placement (mixed-palletize, grid) as well, in case perfect stacking is not required. This would decrease planning iterations and therefore increase cycle time.
5-10 degree object rotation really makes a lot of difference with respect to wrist elbow singularities.
Is there any way to achieve this behavior already?
Thank you very much and kind regards,
Jonathan
Hi Jonathan,
When you are using the picking relaxation, Mech-Viz will attempt each degree one by one until it finds a feasible picking angle, which can increase cycle time, so you may consider reducing the number of attempts. And a long cycle time may also be caused by multiple reasons:
- Your gripper might be too large for the workpieces or inadequately designed, so there are few feasible picking angles for the robot.
- The workpieces may be heavily stacked, which increases the risk of collisions.
- There may be too many MOVEL instructions in the path planning, which can lead to many singular points.
Hi Huan,
thanks for your fast response.
I didn’t mean using the picking relaxation, but a placement relaxation. So I want the path planner to test each degree one by one for the placement operation. (it works very well for the picking part).
I hope I was able to explain it better?
Let me check with my colleague about this and get back to you later : )
Hi Jonathan,
I’ve consulted with my colleague. Unfortunately, Mech-Viz currently does not provide such feature for placement tasks like mixed-palletizing. Plus, rotation relaxation is typically used to avoid collisions between the gripper and the workpieces. If there are no collisions during placement, setting the rotation relaxation won’t do anything.
Hi Jonathan,
- About the very long planning time, based on my actual experience, trying the relaxation only once in each positive and negtive direction yields the best result. Increasing the number of attempts beyond this does not significantly improve the success rate of planning, while due to the excessive number of iterations, it will significantly increase the planning time.
That is to say, you can set the “Attempt range” and the “Step” as the same value (e.g. 10°).
- About the “placement relaxation”, unfortunately it’s not supported for now, but thanks for your insight. We’ll put it on our todo-list, but I cannot guarantee when it will be officially released. We’ll try our best and let you know at the earliest opportunity.
1 Like
Besides, a new feature, “Singularity Avoidance”, will be released in 1.9.0, you can give it a try at that time.
If the Motion Type is Linear move, you can use multilple-segment joint moves to replace a linear move in order to avoid singularities.
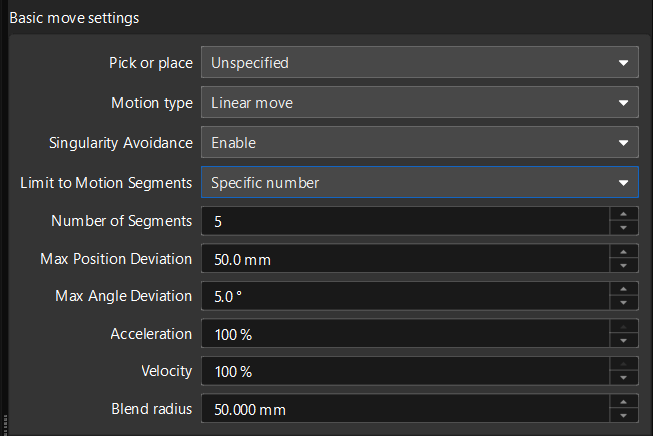
Thank you very much for your explanations.
I believe the placement relaxation would be a great addition for bin picking applications.
The singularity avoidance feature sound interesting, happy to test it for the linear placement moves.
Kind regards,
Jonathan